Smart MCCs: Cut Energy Use Now!
Fault detection and diagnostics (FDD) utilizes the equipment's existing information to identify operational issues in real-time, enabling operators to rectify faults and reduce overall energy consumption in a building.
A meticulously crafted customized motor control system can yield significant returns from the initial installation stages all the way through the entire lifespan of your car wash enterprise. A comprehensive design incorporates sustainable features that address factors such as reducing costs and errors during on-site installation, as well as the capability to record alerts and faults. A carefully planned design provides the adaptability to integrate new car wash equipment as your business expands.
Reduce energy consumption & save money
Trim Costs with Smart MCC Solutions
Does your tunnel controller assist with the management and tracking of electrical faults? Electrical faults, stemming from issues such as faulty wiring, inadequate phase control, and undersized electrical components, are frequently overlooked as potential causes of premature wear and failure in electrical components. Additionally, the frequent switching on and off of motors can generate excess heat and contribute to premature wear, often exceeding the specified motor parameters. Effective energy management can be as straightforward as implementing phase monitoring or configuring the car wash controller to keep motors running if vehicle cycles are too frequent. By logging faults and alerts, whether manually or through your tunnel controller, you can pinpoint the underlying causes of system failures. The subsequent article underscores the significance of fault detection and monitoring.
sgt sudz does MORE
Numerous suppliers provide meters and software to monitor energy usage. These software solutions enable the development of sleek energy dashboards and facilitate access via mobile devices like tablets and smartphones, empowering key personnel to oversee energy consumption. However, what measures are truly necessary to reduce energy usage?
The real key to energy smart buildings is to be able to determine when the energy consuming equipment in a building not operating at maximum efficiency. This is called fault detection & diagnostics (FDD), which uses the existing information available about the equipment, detects in real-time when an operational issue exists that is causing an increase in energy consumption. With this information, the facility maintenance team can schedule corrective action to bring the equipment back into normal energy usage parameters. This sounds almost too logical and seems to make perfect sense, but does take the right software tools and a vision within the facility to take action on the issues identified.
An energy management system will not reduce energy consumption by itself. It is the effective implementation of corrective actions for issues identified in a good FDD system that creates the opportunity for energy savings. In many larger facilities or campus applications, this also requires the application of effective change management. This is due to the natural tendency for operators to go back to the manner in which they have traditionally operated equipment, almost regardless of a what a smart system tells them.
Typical issues identified by a FDD system
There are a wide variety of potential issues that can create abnormal energy consumption without a known mechanical problem. For example, many fan motors and pump motors will be equipped with a hand-off-automatic selector switch. In automatic, the motor will run in response to another control system. In hand, the motor will operate continuously – 24/7/365. This equates to about 20-25 kW hours per day (based on motor efficiency around 70-80%), or > $500 per year in operating cost at $0.08 cost per kWh for a 1HP motor. It is very easy for a motor to be switched to the Hand operating position and be forgotten about.
A good FDD system will look at the real-time operating status of all the motors in a facility and determine if they are operating as designed, or in an unnatural state such as continuously running. A FDD system will have a rule applied to detect the improper setting, such as: After shift end, if the motor operates for greater than 15 minutes continuously, then identify this as a fault. This continuous running fault is logged and available for display in a fault summary table for the facility maintenance depart to take corrective action.
Over-cycling is another potential issue. This means the motor starts and stops too many times within a specified period of time such as per day. This could be caused by faulty setpoints, improperly operating sensors, or improper control settings such as the hysteresis around the setpoint. This type of performance can negatively impact equipment in several ways: shortened equipment life due to the excessive cycling, increased energy consumption especially higher demand when starting, and lack of steady state operation that can decrease overall energy efficiency. A FDD system can detect this type of fault easily by continuously monitoring the number of equipment starts in a 24 hour period.
Another common issue that can impact fans and pumps is inefficient performance as compared to design specifications. All fans and pumps have a performance curve and chart that will indicate expected performance (air output or pump flow rate, for example).
A good FDD System can have the specific information for each fan and pump loaded into a database and then the FDD system can evaluate actual performance against expected performance. A fault in this area could indicate a wide variety of issues such as clogged or partially blocked filters, excessive impeller wear on pumps, improper valve and damper settings, etc. The FDD also five additional benefits to users in addition to detecting operational faults:
- Faults will be logged and summarized in a table for each piece of equipment (see example of a wind turbine).
- Faults will be logged into a database and available for historical analysis. For example, a chart summary of the # of faults per day can be viewed for each piece of equipment.
- A cost for not correcting the fault can be calculated for each fault. This can be used to prioritize work order schedules to correct the most costly fault first and also provides the technician with an expected reason for the fault leading to more efficient corrective actions. With less time spent on diagnosis and more time on corrective actions, the maintenance team is also more productive.
- A good FDD system can be easily adapted and modified to reflect the actual equipment and operational knowledge for each facility. It is also easily modified when new situations occur and unexpected operational situations occur allowing for the continued development of an equipment smart system.
- A good FDD system does not require the change out of any existing hardware or systems—it is designed to support almost any type of communications protocol and interface with any hardware platform.
FDD is proven technology and is being widely applied in building automation systems (BAS). There are documented examples where a building energy consumption has been reduced by ~15% as a result of the operational intelligence provided by the FDD system. These FDD systems have been implemented without changing anything related to existing control systems and takes advantage of the data points that already exist within the existing control system.
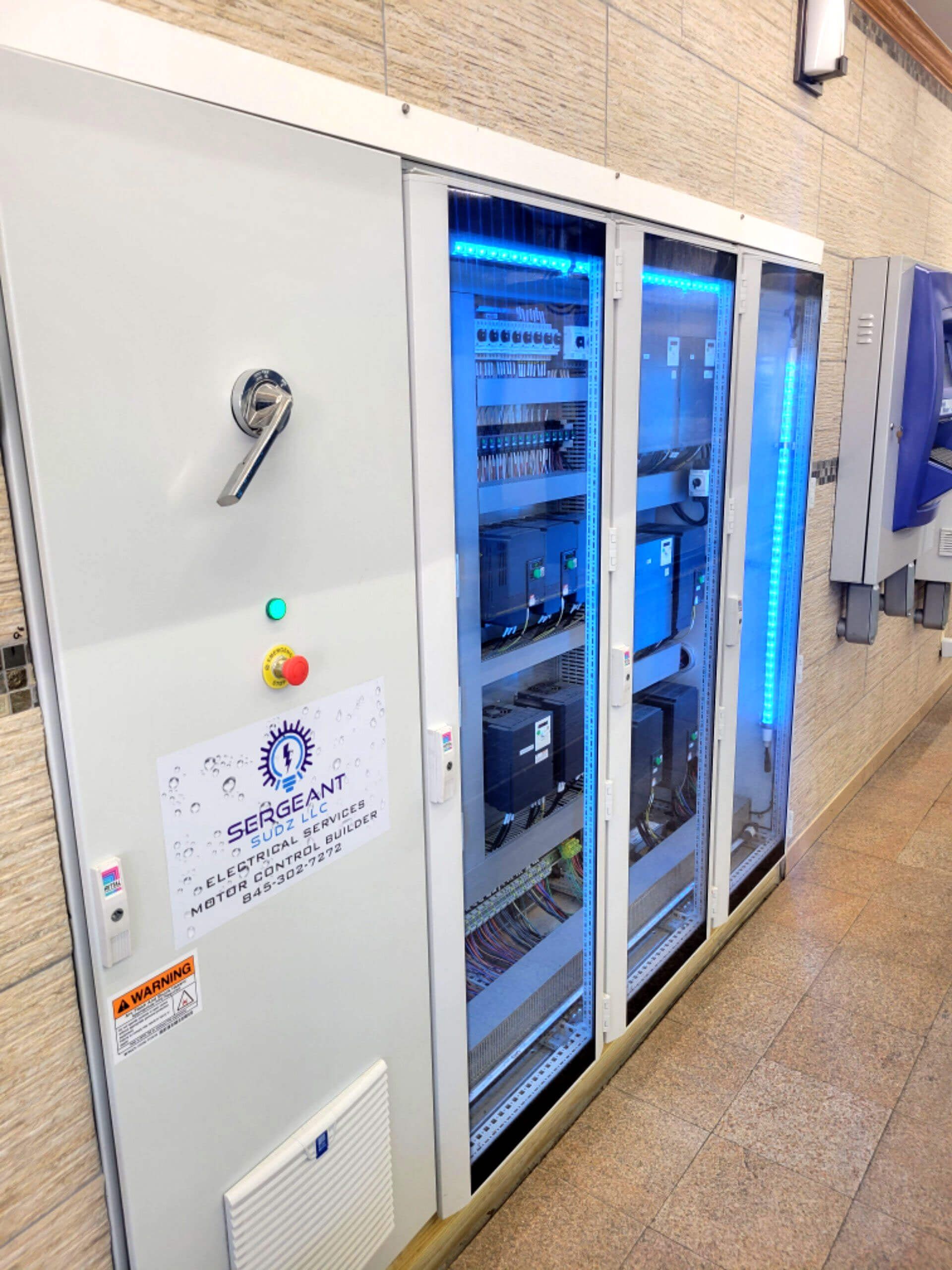
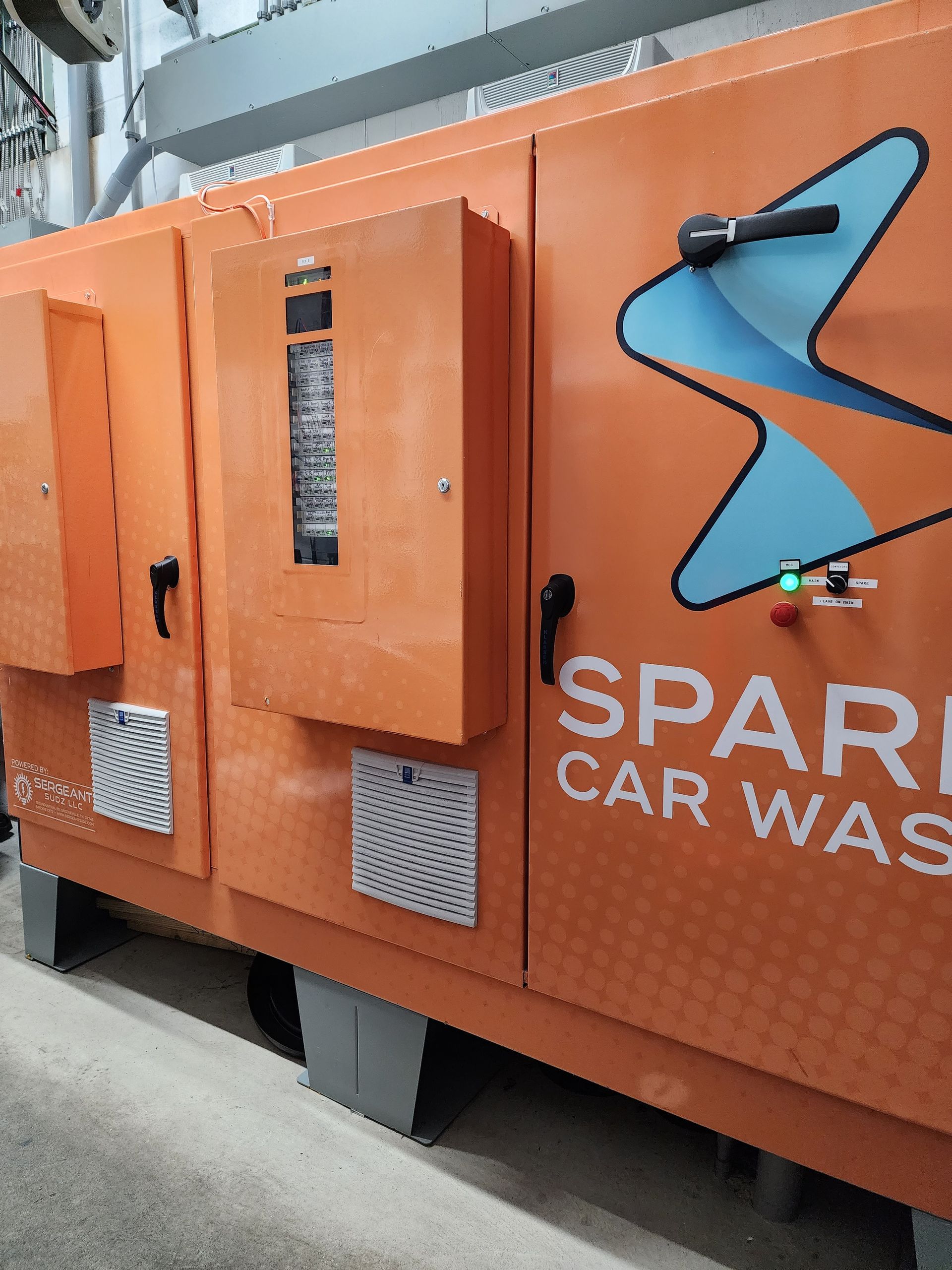
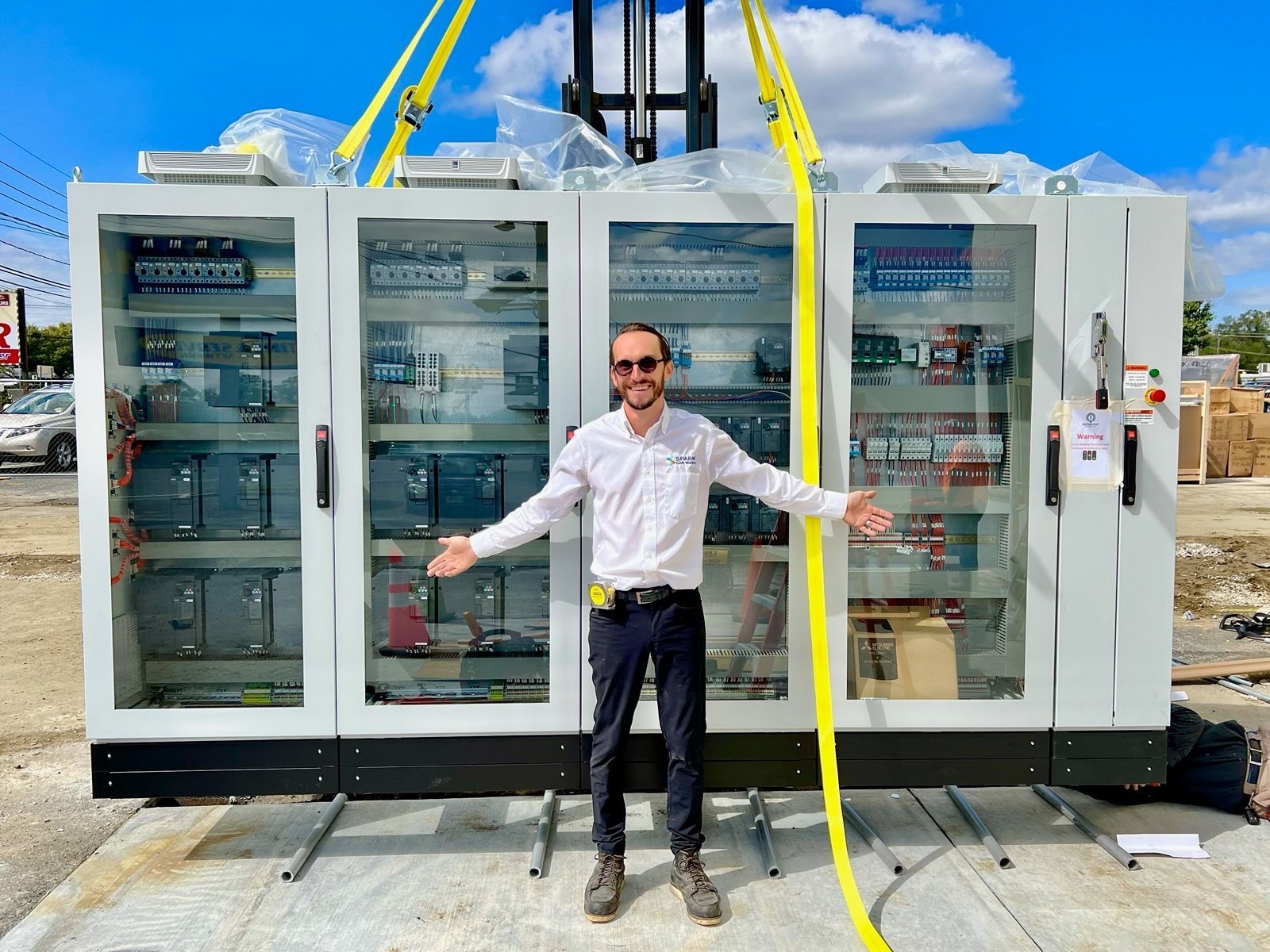